Volkswagen Tiguan Service and Repair Manual: General Information
Vehicles with a high voltage system (hybrid vehicles)
Observe all of the additional warnings for all work performed on vehicles
with the high voltage system.
WARNING
Risk of unintended engine start
The ignition must be turned off and the ignition key must remain outside of
the vehicle when working on vehicles with a high voltage system.
WARNING
Handling high voltage cables:
- Do not stand on or place tools on high voltage cables and their
components as it may damage the cable insulation.
- Never bend or kink high voltage cables forcefully as it may damage the
cable insulation.
- The round high voltage connectors are color coded with an external color
ring and are mechanically coded using the guide- or code tabs. Always make
certain that the coding matches when connecting the round connector in order
to avoid any mechanical damage the high voltage connector.
WARNING
There is a risk of electrocution from damaged high voltage components.
Observe the following when working around high voltage components and high
voltage wires:
- Never work around high voltage components and cables with cutting,
deformed, or sharp edged tools, or heat sources such as welding or soldering
tools, heated air, and thermal glue.
- Inspect the high voltage components visually before beginning.
- Perform a visual inspection of the Electric Drive Power and Control
Electronics -JX1-, the Electro-Drive Drive Motor -V141-, the Electrical A/C
Compressor -V470- and the high voltage lines when working in the engine
compartment.
- Perform a visual inspection of the high voltage lines and covers when
working on the underbody.
- Perform a visual inspection of the high voltage lines and the Electrobox
with the High Voltage System Maintenance Connector -TW- when working in the
luggage compartment.
- Perform a visual inspection on all of the potential equalization cables.
Observe the following items when performing the visual inspection:
- The components do not display any signs of external damage.
- The high voltage cable insulation and the potential equalization cables
are not damaged.
- The high voltage cables do not display any abnormal deformations.
- Every high voltage component is marked with a red warning label.
If it is necessary to perform work in the vicinity of high voltage
components, perform a "visual inspection" of the high voltage components and
cables for damage and follow the "general warnings when working on the high
voltage system".
If it is necessary to perform work on the high voltage components, disable
the high voltage system.
Caution
- If it is suspected that chemicals were added to the refrigerant circuit
to seal leaks, do not connect the A/C service station and do not extract the
refrigerant.
- Chemicals that seal leaks in the coolant circuit form deposits that
affect the function of the A/C system and lead to failure of the A/C system
and the A/C service station.
- Remind the customer that the refrigerant circuit contains substances
that VW has not approved. As such, the refrigerant circuit cannot be
flushed. It is only possible to service the refrigerant circuit by replacing
all the components which come in contact with this material.
Note
- VW does not approve the use of chemicals to seal leaks in the
refrigerant circuit.
- Chemicals used to seal leaks in the refrigerant circuit often react with
air and the moisture in it. They cause deposits in the refrigerant circuit
and the A/C service station and malfunctions in valves and other components
that they come in contact with. These deposits cannot be removed completely
from the components, even by flushing. It is only possible to service the
refrigerant circuit by replacing all the components which come in contact
with this material.
- Chemicals used to seal leaks in the refrigerant circuit usually cannot
be detected from outside. The label that should be applied to identify it is
often missing. Therefore be careful when working with if you do not know its
service history.
- Refrigerant circuit must be flushed with refrigerant R134a in order to
force out contaminants (e.g. abraded material from a malfunctioning A/C
compressor) as well as old refrigerant oil as efficiently and as cleanly as
possible and without the need for extensive work.
For vehicles with an electrically-driven A/C compressor, pay attention to the
notes for replacing the Electrical A/C Compressor -V470-. If there is damage on
the A/C compressor electronics, the refrigerant circuit must not always be
cleaned.
The refrigerant circuit should be flushed with refrigerant R134a if:
- dirt or other contamination is in the refrigerant circuit.
- vacuum reading is not maintained on evacuating a leak-free refrigerant
circuit (pressure build-up due to moisture in refrigerant circuit).
- refrigerant circuit has been left open for longer than normal (e.g.
following an accident).
- If pressure and temperature measurements in the refrigerant circuit
indicate the likelihood of moisture in the circuit.
- In the event of doubt about the amount of refrigerant oil in the
circuit. If the A/C compressor should be reinstalled, the refrigerant should
be drained from the compressor via the oil drain plug. To facilitate this,
the ribbed belt pulley or magnetic clutch plate on the A/C compressor should
be rotated by hand. After flushing, the entire quantity of refrigerant oil
specified by vehicle-specific repair manual should be added to the
refrigerant circuit (50 grams directly in the A/C compressor). Note
additional oil quantity for systems with a second evaporator.
- A/C compressor had to be replaced on account of internal damage (e.g.
noise or no output).
- stipulated by the vehicle-specific repair manual following replacement
of certain components.
- Another compressor with different refrigerant oil should be installed.
Tools required
- A/C Service Station with Flushing Device -VAS6381- or Air Conditioning
Flush Tool -VAS6337-. The auxiliary function "Flush refrigerant circuit" and
the refrigerant circuit flushing device required for it are present on these
A/C service stations. Refer to Special Tools Catalog.
- Refrigerant Circuits Adapter Set 1 -VAS6338/1-.
- Refrigerant Circuits Adapter Set 2 -VAS6338/50-.
Note
- If neither of the two A/C service stations listed above are available
for use in the workshop, A/C Service Station with Flushing Device
-VAS6336/1- or Air Conditioning Flush Tool -VAS6337/1- (depending on the
workshop A/C service station version) (min. 7 kg refrigerant R134a in
refrigerant bottle) can also be used to flush the refrigerant circuit.
However, the flushing procedure must then be performed manually.
- In vehicles with screw-connections on refrigerant circuit, A/C Adapter
Set - Adapter 1 -VAG1785/1- through A/C Adapter Set - Adapter 2 -VAG1785/8-
from the Refrigerant Circuits Adapter Set 1 -VAS6338/1- or Refrigerant
Circuits Adapter Set 2 -VAS6338/50- may be used. In vehicles with
screw-connections on A/C compressor and on accumulator, two of the A/C
Adapter Set - Adapters 8 -VAG1785/8- are required.
- A Refrigerant Circuits Adapter Set 2 - Adapter 31 -VAS6338/31- with 5/8
-18 UNF connections and large internal diameter can be found in the adapter
chests in order to be able to bridge components (it is commercially
available).
Preliminary work
- Discharge refrigerant circuit.
- Remove A/C compressor. Refer to Heating, Ventilation & Air Conditioning.
On a vehicle with restrictor and reservoir.
- Remove restrictor (specific to vehicle) and reconnect refrigerant pipes
to each other. Refer to Heating, Ventilation & Air Conditioning.
- Remove reservoir (specific to vehicle). Refer to Heating, Ventilation &
Air Conditioning and connect refrigerant pipes to each other (to do this,
use adapter and Refrigerant Circuits Adapter Set 1 - Adapter 31
-VAS6338/31-) from Refrigerant Circuits Adapter Set 1 -VAS6338/1-.
Note
The reservoir could be flushed, but it requires too much refrigerant due to
its large volume. When this refrigerant is extracted, the reservoir ices up
severely and this prolongs the extraction process significantly.
On a vehicle with expansion valve and receiver/dryer.
- Remove receiver/dryer. Refer to Heating, Ventilation & Air Conditioning
(specific to vehicle, not required for all vehicles) and connect refrigerant
pipes to each other (for this, use adapters and Refrigerant Circuits Adapter
Set 1 - Adapter 31 -VAS6338/31-).
- Remove expansion valve. Refer to Heating, Ventilation & Air Conditioning
(specific to vehicle) and install the adapter for it.
Note
If no suitable adapter for the expansion valve is available in Refrigerant
Circuits Adapter Set 1 -VAS6338/1- or Refrigerant Circuits Adapter Set 2
-VAS6338/50-, the remove expansion valve can also be drilled open (the expansion
valve must be replaced with a new one).
Caution
- Make sure the sealing surfaces on the expansion valve are not damaged
when drilling open.
- Otherwise refrigerant leaks out.
Note
- Several components are to be removed from expansion valve before
drilling open.
- Expansion valves are available in different versions. For version
-A-, components -B-,
-C- and -D- must
be removed. Then separate regulating element -E-
from component -D-. Then drill open expansion
valve in area -F- using a suitable drill (6 mm
diameter).
- For version -G-, parts
-H-, -I- and
-K- must be removed and then drill open area
-L- using suitable drill (6 mm diameter).
- Clean the drilled open expansion valve of residue from the work
(shavings).
- Install parts -B-,
-C- and -D- for version
-A- or -H- for
version -G-.
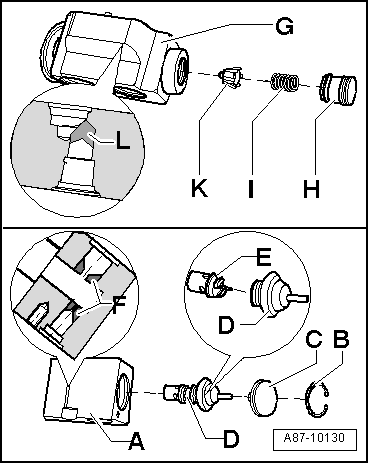
Note
In vehicles with two evaporators, the circuit to the second evaporator must
be disconnected from circuit of the first evaporator and must be flushed via a
separate work procedure.
Drilling open the shut-off valve.
Note
- Two shut-off valves are required for flushing the refrigerant circuit/
If the Refrigerant Circuits Adapter Set - Shut-Off Valve -VAS6338/42- is not
available to flush the refrigerant circuit, than a shut-off valve is to be
drilled out, for example.
- Remove the solenoid coil -A- and the
solenoid valve -B- before drilling open.
- Drill open the shut-off valve -C- using a
suitable drill (diameter of the drill for example 5.0 mm).
- Clean the shut-off valve -C- from shavings
produced by drilling -D-.
- Install the solenoid valve -B- with the
seals belonging to it -E- on the drilled open
shut-off valve -C-.
Flushing
- Check refrigerant quantity in the refrigerant cylinder, there must be at
least 7 kg of refrigerant R134a.
Note
If necessary, switch on the heater installed on the refrigerant cylinder for
30 minutes before the first flushing procedure. This increases pressure in the
refrigerant cylinder and accelerates charging of the flushing circuit.
- Evacuate the A/C service station old oil container.
- Connect the supply hose (high pressure side) of A/C service station to
the low pressure line leading to the A/C compressor (line with larger
diameter) using an adapter.
- Connect return hose (low pressure- or intake side) of A/C service
station to output of refrigerant circuit flushing device.
- Connect the input on the refrigerant circuit flushing device to the high
pressure line leading to the A/C compressor (line with smaller diameter)
using an adapter.
Note
- Components are always (with the exception of the electrically-driven A/C
compressor) flushed in the opposite direction of refrigerant flow when the
A/C system is operating.
- While flushing, contaminants from the refrigerant circuit enter the
refrigerant circuit flushing device and the A/C service station and are
absorbed by the filters and dryers installed there. Depending on the
contaminant, these components are to be replaced in shorter intervals in
line with operating instructions for A/C service station or refrigerant
circuit flushing device.
- The filter in the refrigerant circuit flushing device depends on the
type and degree of contamination in the flushed refrigerant circuit. It
should be replaced after 2 flushing cycles, at the most. If a heavily
contaminated refrigerant circuit is flushed (the refrigerant oil from the
circuit is black and viscous or there are many shavings in the refrigerant
circuit), the filter should be replaced after flushing. With a refrigerant
circuit heavily contaminated in this way, it is wise to flush the circuit
again after changing the filter.
- Depending on the type of contamination, dirt (old refrigerant oil and
abraded material from A/C compressor) is deposited on the viewing glass(es).
Clean viewing glass(es) after flushing and flush the refrigerant circuit
once more with one flushing procedure as a check.
- Fluid refrigerant cannot be conducted with the necessary speed through
the expansion valve, restrictor and desiccant bag of certain
receiver/dryers, therefore these components must be removed and replaced by
an adapter. Refer to Heating, Ventilation & Air Conditioning.
- Adapters for connecting A/C service station and for bridging certain
components of refrigerant circuit.
- Switch on the service station and flush the refrigerant circuit
(duration for one flushing cycle with three flushing procedures is
approximately 1 to 1.5 hours for about 4Kg of coolant R134a).
Note
- Perform flushing of refrigerant circuit according to operating
instructions of the A/C service station.
- Depending on A/C service station version, the old oil container holds
only approximately 125 cm 3 of refrigerant oil.
In the event a system with a larger volume of refrigerant oil must be
flushed, it may be necessary to empty the old oil container after the first
flushing procedure of a flushing cycle.
- Observe the refrigerant which flows back from the refrigerant circuit.
The refrigerant circuit is only clean when the refrigerant flows clear and
completely colorless through the viewing glass(es) on the flushing device in
the A/C service station.
- When flushing, the complete amount of refrigerant oil is washed out of
the refrigerant circuit (except for minor remains which can be disregarded).
- If contamination is especially severe, it may be necessary to perform
the flushing cycle twice (two flushing cycles with three flushing operations
each). Before the second flushing cycle, the filter on the flushing device
must be replaced.
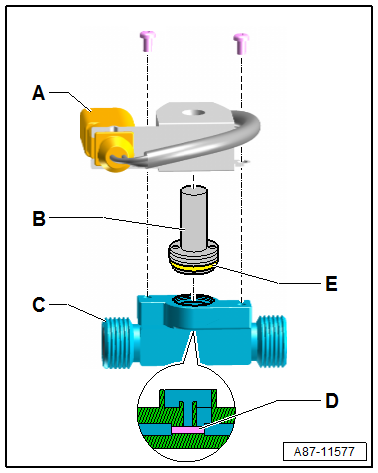
Sequence of flushing procedure (sequence occurs automatically according to
the A/C service station program)
- After switching on, the flushing circuit (refrigerant circuit with
connecting hoses and refrigerant circuit flushing device) is first evacuated
and the refrigerant circuit is simultaneously checked for leaks. Depending
on A/C service station version, it is possible that manually switching to
advance the program is required.
- A prescribed amount of refrigerant (e.g. 4 kg) is filled into the
evacuated flushing circuit via the high pressure side of the A/C service
station (opposite the normal direction of flow during normal A/C system
operation and thus on the low pressure side of vehicle refrigerant circuit).
Depending on the version of the A/C service station, refrigerant is added
until the flushing circuit is completely full. This can be detected by e.g.
refrigerant no longer flowing in after a certain period of time.
- After the prescribed quantity of refrigerant has been filled, for
example. the heater for the refrigerant circuit flushing device is switched
on (only in the event the refrigerant is extracted in gaseous form from the
refrigerant circuit flushing device), depending on version of A/C service
station and refrigerant circuit flushing device.
- After the refrigerant has been extracted, the heater on the refrigerant
circuit flushing device (if applicable) switches off, the refrigerant
circuit may be evacuated again (depending on the version), and the
refrigerant oil extracted from the refrigerant circuit is separated by the
A/C service station after evacuating.
- The sequence of filling refrigerant, extracting (and evacuating) is
repeated twice (performed a total of three times).
- After the third extraction, the flushing circuit is evacuated depending
on the version of the A/C service station.
- After the flushing cycle has ended, check the viewing glass(es) on the
flushing device. If they are dirty, clean them according to the instructions
for the flushing device or A/C service station. Perform one addition
flushing cycle as a check. One flushing procedure is sufficient
(approximately 30 min.)
- Check pressure in refrigerant circuit, there must be no positive
pressure in the refrigerant circuit (evacuate refrigerant circuit briefly
once more if necessary).
- Disconnect A/C service station connections from vehicle refrigerant
circuit. There must be no positive pressure in the refrigerant circuit.
- Replace these vehicle-specific components.
- Restrictor and reservoir
- Expansion valve and receiver/dryer or dryer cartridge in receiver/dryer
- Refer to Heating, Ventilation & Air Conditioning and the Parts Catalog.
- Depending on the complaint, replace A/C compressor. Refer to Heating,
Ventilation & Air Conditioning and the Parts Catalog or drain the remaining
refrigerant oil from the removed A/C compressor. Refer to
→ Chapter "Components, Replacing" (replace refrigerant circuit
components) and refill the prescribed quantity of fresh refrigerant oil.
Refer to the vehicle-specific repair manual.
Note
- A certain prescribed quantity of refrigerant oil is in the A/C
compressor original part. If the vehicle has two evaporators, then the
refrigerant circuit requires a specific quantity of refrigerant oil. Refer
to the vehicle-specific repair manual.
- If the A/C compressor is not be replaced, the quantity of refrigerant
oil in the A/C compressor must be topped off to the prescribed capacity
(tilt the refrigerant oil out and refill the prescribed quantity into the
A/C compressor or refrigerant circuit). Refer to
→ Chapter "Components, Replacing" (replacing refrigerant circuit
components) and vehicle-specific repair manual.
- Completely reassemble the refrigerant circuit. Refer to Heating,
Ventilation & Air Conditioning.
- Evacuate and recharge refrigerant circuit according to specification.
- Start up A/C system according to specification.
Note
The arrows in the following illustrations show the direction of
refrigerant flow while flushing. During flushing, refrigerant flows in the
opposite direction than during A/C system operatio ...