Volkswagen Tiguan Service and Repair Manual: Driver Assistance Systems Front Camera -R242-
General Information
Note
If the camera can no longer recognize the lane markings due to poor
visibility, this could be caused by:
- The camera visual field is dirty or icy. If that is the problem, it
should be corrected.
- The camera view field in fogged over.
If the camera lens is obstructed by a lot of dirt on the inside, then lens
must be cleaned by hand. To do this, remove the control module and the lens, and
clean the windshield using cleaning solution. Remove the control module and lens
screen.
The calibration must be correct or the Driver Assistance Systems Front Camera
-R242- to function correctly.
The Driver Assistance Systems Front Camera -R242- must be calibrated again
for the following reasons:
- "No or incorrect basic setting/adaptation" is stored in the event
memory.
- The Driver Assistance Systems Front Camera -R242- was replaced.
- The windshield was replaced or removed.
- The rear axle toe was adjusted.
- Work was performed on the chassis which influences the body height.
- The vehicle level sensor was readapted on vehicles with damping
regulation.
Note
- Before calibrating the driver assistance systems front camera, check the
DTC memory and correct any faults.
- To calibrate the driver assistance systems front camera, the geometric
drive axle of the vehicle must be determined. It serves as a reference point
for the Setting Device Basic Set -VAS6430/1-.
- The driver assistance systems front camera may only be calibrated using
alignment equipment approved by VW/Audi.
- Only the Setting Device Basic Set -VAS6430/1- may be used to calibrate
the driver assistance systems front camera.
Driver Assistance Systems Front Camera, Adjusting
Special tools and workshop equipment required
- Setting Device Basic Set -VAS6430/1-
- Wheel Alignment Computer
- Vehicle Diagnostic Tester
Note
- The Driver Assistance Systems Front Camera -R242- must fit correctly in
the retainer.
- The camera viewing range must be clean and unobstructed.
- Before driving the vehicle onto the vehicle alignment platform, make
sure there is sufficient space between the center of the wheel hub on the
front wheels and the Setting Device Basic Set -VAS6430/1-.
- The distance between the Setting Device Basic Set -VAS6430/1- and the
center of the wheel hub on the front wheels must be 1,500 mm +- 25 mm.
- If there not enough space, back the vehicle onto the vehicle alignment
platform so that there will be enough space.
- The calibration board must be positioned in the center of the setting
device.
- Check the DTC memory before calibrating. Erase any entries if necessary.
- Follow the test requirements for an axle alignment.
- Drive the vehicle onto the vehicle alignment platform.
- Connect the battery charger.
- Connect the Vehicle Diagnostic Tester to the vehicle. (Guide the
diagnostic cable through the open window.)
Note
During the calibration procedure, make sure all the vehicle doors remain
closed and the vehicle exterior lighting is switched off.
- Position the front wheels so they are straight.
- Select calibrating the driver assistance systems front camera in the
wheel alignment computer.
- Install the quick clamps on all four wheels.
- Mount the measuring sensors on the wheels.
- Perform a rim run-out compensation on the rear wheels.
- Bounce the vehicle.
- Measure and record the ride height at all four wheels.
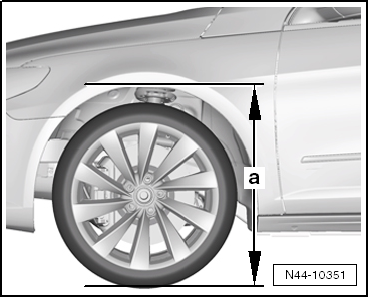
Note
- The Setting Device Basic Set -VAS6430/1- must not be moved on the
calibration beam.
- The alignment stand must be in the lowest level position for the next
step.
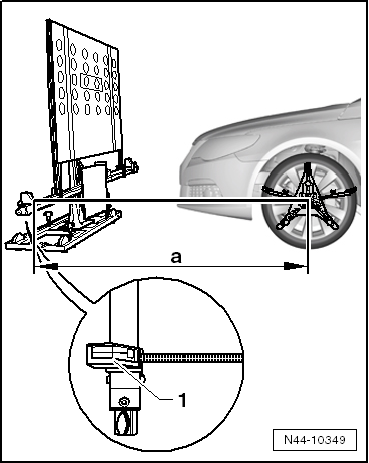
- Rotate the Setting Device Basic Set -VAS6430/1- upward just enough so
that the calibration beam is parallel to the center of the measuring sensors
on the front wheels, so that it is possible to correctly measure the
distance measuring unit -1-.
- Distance measuring unit with spring tape measure and mounting pin
- Position the Setting Device Basic Set -VAS6430/1- at a distance
-a- of 1500 mm +- 25 mm from the center of the
wheel hub on the front wheels to the beam on the Setting Device Basic Set
-VAS6430/1-.
Caution
- Distance -a- 1,500 mm +- 25 mm must be
measured on both side of the vehicle and then the Setting Device Basic Set
-VAS6430/1- must be aligned.
- Distance -a- must be the same on both sides
of the vehicle.
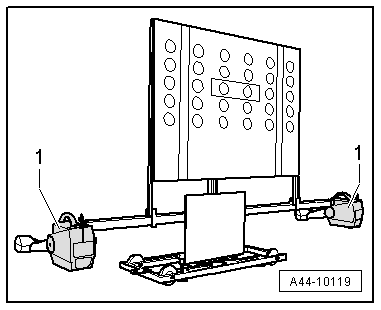
- Mount the front wheel measuring sensors -1-
to the Setting Device Basic Set -VAS6430/1-.
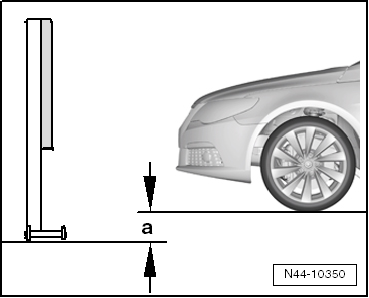
- Determine the height value -a- between the
Setting Device Basic Set -VAS6430/1- contact patch and the wheel contact
surface on the vehicle alignment platform and enter it in the alignment
computer.
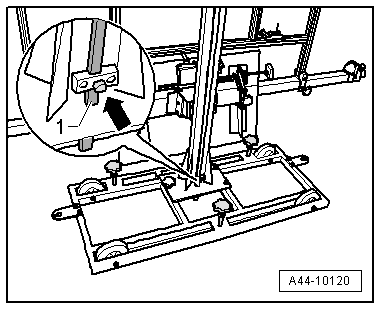
- Loosen the clamping bolt -arrow- and place
the measuring bar -1- on the floor.
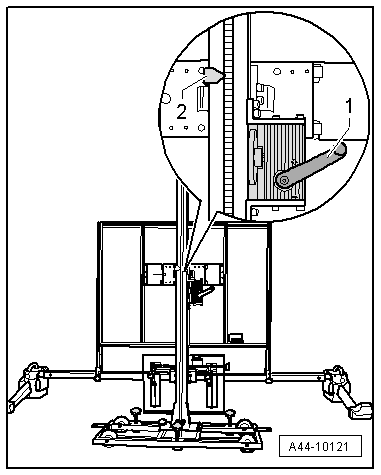
- Turn the crank -1- to adjust the
Calibration Board For Lane Guard System -VAS6430/4- to the height
specification -2- and then make a note of it.
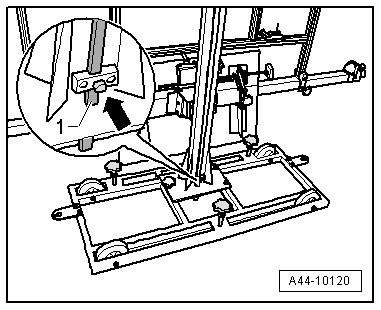
If the specified height was reached, then the measuring bar
-1- must be pushed slightly forward and secured
with the locking bolt -arrow-.
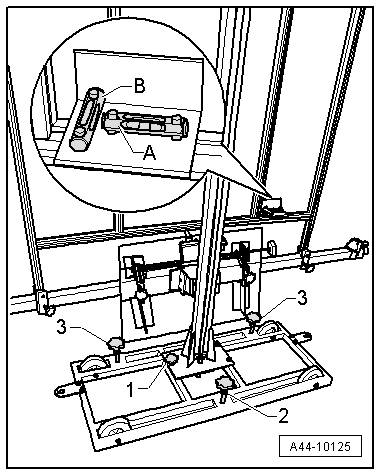
- Level the bubble level -A- using the
adjusting screw -1-.
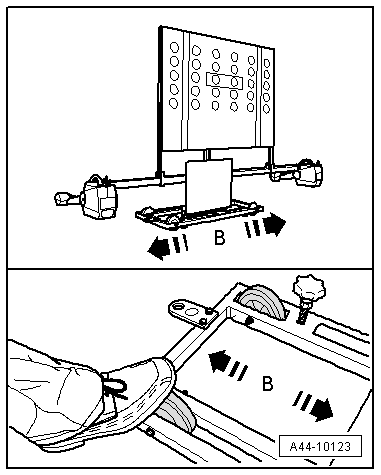
- Slide the Setting Device Basic Set -VAS6430/1- to the side
-arrows B-, until the display in the wheel
alignment computer is in the tolerance range.
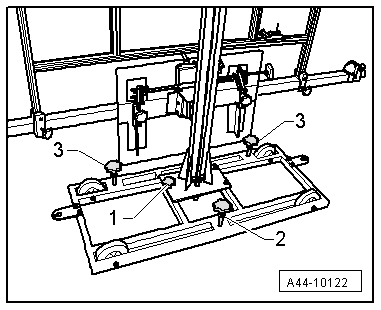
- By gently turning the adjustment screws -2 and 3-
secure the Setting Device Basic Set -VAS6430/1- from rolling away.
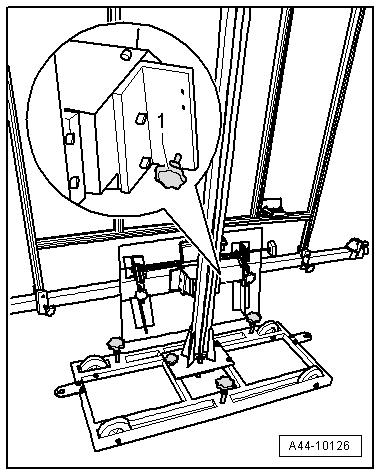
- Turn the precision adjustment screw -1-
until the display on the wheel alignment computer is located within the
tolerance range.
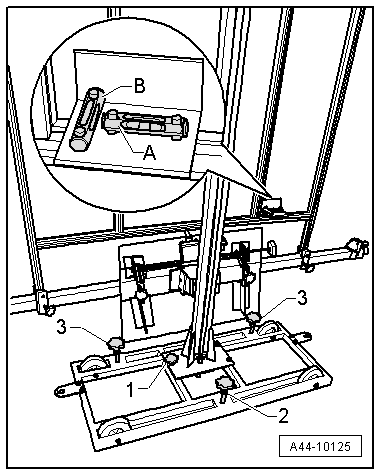
- Level the bubble level -A- using the
adjusting screw -1-.
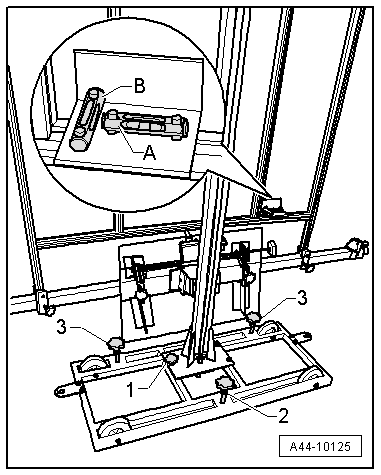
- Level the bubble level -B- using the
adjusting screws -2 and 3-.
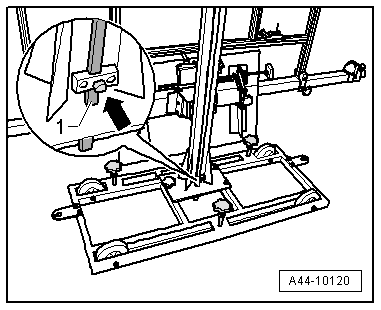
- Loosen the clamping bolt -arrow- and place
the measuring bar -1- on the floor.
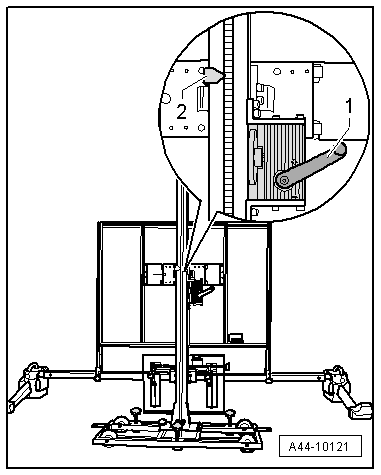
- Check specified height -2- one more time
and adjust if necessary.
If the specified height was reached, then the measuring bar
-1- must be pushed slightly forward and secured
with the locking bolt -arrow-.
Perform any Subsequent Work using the Vehicle Diagnostic Tester.
- Switch the ignition on.
- Select "Guided Fault Finding" on the Vehicle Diagnostic Tester.
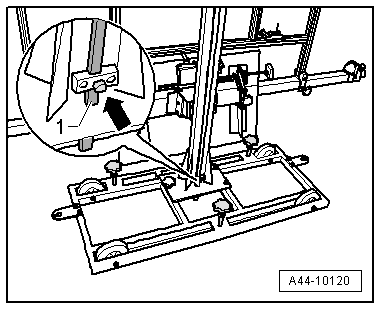
Body (Repair Group 01;27;50 through 97)
Electrical System (Repair Groups 01, 27 and 90 through
97)
01_OBD-capable systems
Driver Assistance Systems Front Camera -R242-
Driver assistance system camera, functions
A5 - Calibrate the control module (Repair Group 44)
Follow the instructions on the screen to perform the calibration.
Note
Next, in guided fault finding, determine the height of the body.
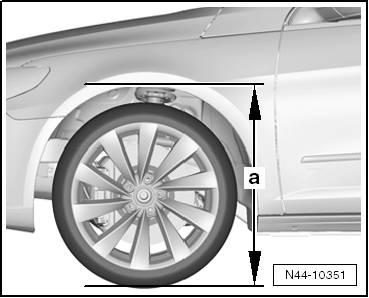
- Enter the recorded ride heights.
Special Tools
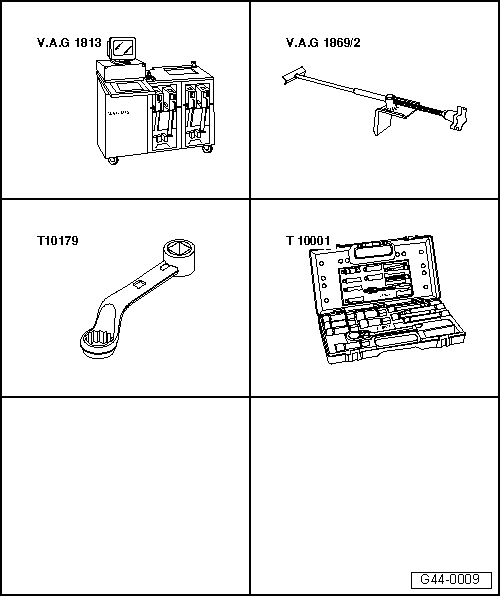
Special tools and workshop equipment required
- Wheel Alignment Computer -VAG1813- or VW/Audi approved wheel alignment
devices
- Brake Pedal Actuator -VAG1869/2-.
- Insert Tool - 18mm -T10179-
- Shock Absorber Set -T10001-
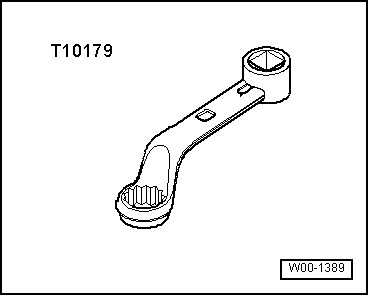
- Insert Tool - 18mm -T10179-
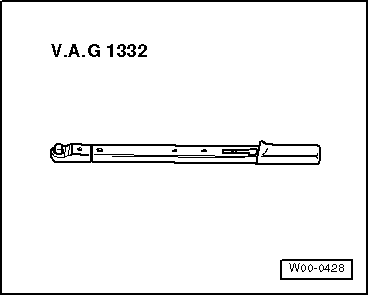
- Torque Wrench 1332 40-200Nm -VAG1332-
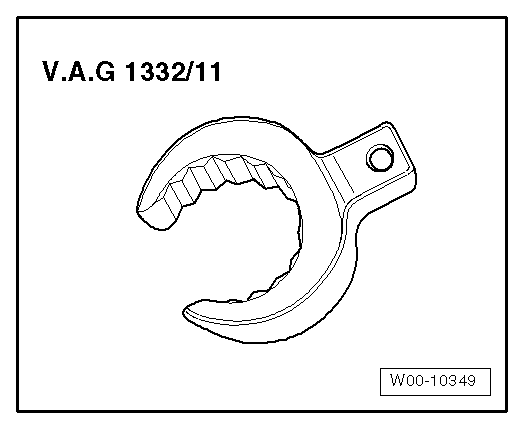
- Torque Wrench 1332 Insert - Open Ring Wrench - 24mm -VAG1332/11-
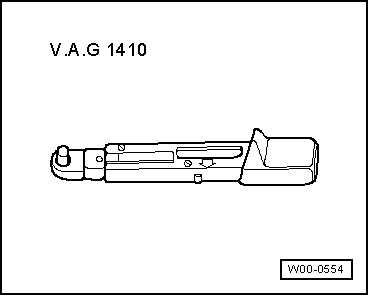
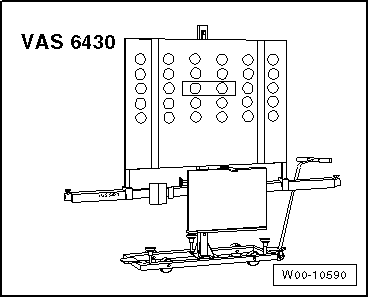
- Setting Device Basic Set -VAS6430/1-
- Wheel Alignment Computer
- Vehicle Diagnostic Tester
Vibration Causes
There are many causes for vibration. Vibration can also be caused by tire
wear, among other things. Tire wear caused by driving does not always develop
evenly over the entire tread. ...